工業(yè)大數(shù)據(jù)是個大號尺寸的衣服 我們似乎陷入了大數(shù)據(jù)數(shù)據(jù)焦慮癥,非常急于從工業(yè)大數(shù)據(jù)攫取金礦。然而,實際上,工人身邊很多的小數(shù)據(jù),直接決定了一個企業(yè)的效率。很簡單,產品的價值由客戶決定的,而產品的價值組成,則是由流程決定。流程中存在著大量的“小數(shù)據(jù)”,正是企業(yè)產品真正的價值。 產品是通過流程才能提供給客戶的。從原材料到成品的流程中,經過流程里面的各種各樣的機器和人的活動之后,實現(xiàn)了從原材料到客戶需要的產品的價值的附加,而客戶愿意為之付錢的流程中的活動,才是有價值的活動。但是在流程中,除了有價值的活動之外,還存在其他兩種活動,一種是純粹的浪費,一種是雖然沒有價值但是不得不作的活動。如圖1所示。這是典型的精益生產思想。 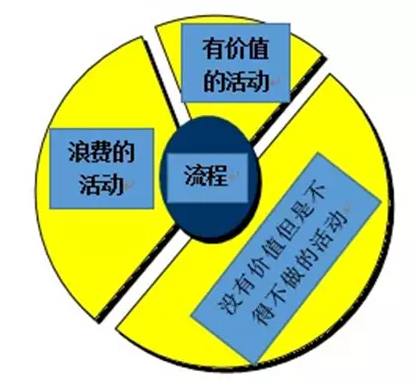
圖1 產品流程 許多浪費的現(xiàn)象,其實在生產一線都是各種各樣司空見慣的“小”數(shù)據(jù)。比如說:員工上班后等待原材料的時間是多少分鐘,等待機器穩(wěn)定運轉起來的時間是多少分鐘;搬運工的具體搬運次數(shù),具體距離,耗費時間都是需要考慮的問題;作為工人,重(chong)工有缺陷的產品的具體數(shù)量,重工耗費的具體時間,重工用掉的物料的種類和數(shù)量;前面的流程干的太快,后面的流程機器不給力,兩個流程之間堆起了小山一樣等待生產的產品的具體數(shù)量;庫房里面的原材料的具體數(shù)量,成品的具體數(shù)量;廠房太大,從這臺機器到另外一臺機器隔著幾十米的距離,產品在兩臺機器之間搬來搬去;送貨工每天都要往返幾公里在車間里面,走了好幾萬步,這也是小數(shù)據(jù)。 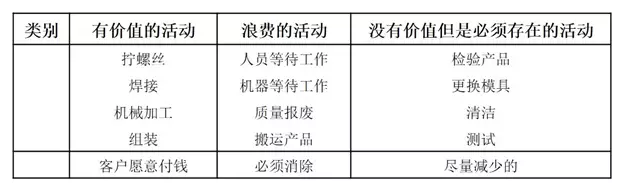
表1 三種不同的價值流程 再細化一點,在一個機器上面生產了幾種不同的產品,每個產品都要更換不同的模具,更換了多少次,每次用掉了多少時間?更換后為了調整模具耗費的時間;為了調整模具而試做的產品的數(shù)量;生產的產品拿到質量檢測部門作首件測試再反饋回來合格的結果的時間。 各種各樣的數(shù)據(jù)如同汪洋大海,但是企業(yè)的管理層卻看不到,因為他們看到只是財務的數(shù)據(jù);車間的工人們被數(shù)據(jù)淹沒著卻毫無感覺,因為沒有人告訴他們,這些數(shù)據(jù)到底意味著什么? 隱藏的工廠與隱蔽的數(shù)據(jù) 美國米勒先生,1992針對企業(yè)沒有被認知到的程序,稱之為“隱藏的工廠”。 然而直到今天,這樣的“隱藏的工廠”還在企業(yè)中大量中不曾被發(fā)現(xiàn)。 流程中存在的大量浪費,同樣可以看作是大量的沒有挖掘出來的流程價值,而這些價值,可以看作是構成了一個隱形工廠。后面有一個例子可以看到,原來10天的產出時間,如果通過流程改善,縮短到2天,就等于原來10天的產出,在同樣的時間里面翻了4翻,何止是多了一個工廠呢? 很多隱蔽的數(shù)據(jù),比如說,每個產品檢驗的時間,同一個失效模式,在不同的生產流程被重復檢驗的次數(shù);作清潔用的時間,擦拭產品或者機器的時間,這些也統(tǒng)統(tǒng)是浪費的現(xiàn)象帶來的數(shù)據(jù)。 現(xiàn)在企業(yè)非常樂于上自動化生產線,其實最隱蔽的浪費數(shù)據(jù)莫過于自動化連續(xù)生產設備里面的數(shù)據(jù)?雌饋,一摁按鈕,機械手夾起產品,放在機器上面,然后機器開始加工,每天機械手夾起幾千個產品;或者自動化的傳送帶把產品送到這里,送到哪里,每天送上幾萬個產品;更高級的是AGV小車,拖著物料在車間里跑來跑去,一天跑個幾十趟。 然而,不管是人在傳送還是機器在傳送,不管是機械手上下料,還是人工上下料,如果是浪費的動作,那么都不是有價值的工作,而精益思想對于浪費的概念定義里面,搬運—是定義為浪費的。 這些數(shù)據(jù)也都是精益需要的數(shù)據(jù),都是可以量化浪費的精益數(shù)據(jù)。這些數(shù)據(jù),才是工人和企業(yè)領導者們應該實實在在,時時刻刻需要去管理和關心的數(shù)據(jù)。 1%的增值時間,其他時間工廠在空轉 純粹的生產時間,也即產品增值的時間在整個流程占有比例非常小,不到5%,有的不到1%;大量的流程時間,是由于效率低、沒有計劃甚至浪費的等待時間所組成。 就是說,工廠95%的時間,都是在空轉——這是一種觸目驚心的工廠空心化。 例如對一個客戶每天需求400個產品的生產流程進行分析,產品經過機械加工20秒,裝配40秒和檢驗包裝20秒,一共三個流程,針對每一個產品來說,真正被增值的時間只有短短的80秒,但是由于大量的中間在制品和庫存的原材料及成品的存在,加在一起有4000個產品分布在整個生產線上,這就會導致在生產流程中等待的時間的總和要10天,也就是說,如果有一個零件的原材料在這個時候進入工廠的話,那么要等到10天之后,才能被送到客戶的手中,然而在這10天的等待過程中,這個零件真正被增值的時間只有短短的80秒,其他的時間,都是在無謂的等待。 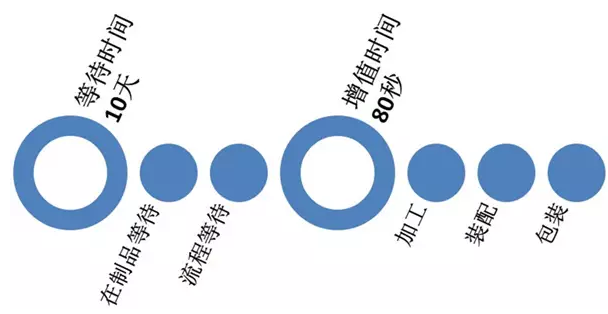
圖2 生產效率 生產效率,取決于流程鏈的復雜程度、交接點的數(shù)量,以及單個流程的不同類型。低流程消耗的資源 (無計劃的等待和停泊時間等)要遠遠大于生產效率所消耗的資源。 在生產線上,更重要的是流程的交接點和在線庫存點,這才是吞嚙時間的黑洞。 上述分析同樣可以看出,單純更新機器設備,對生產效率的改善的效果是微乎其微的,全部改掉也只有80秒;只有把流程中的等待的在制品的數(shù)量減少,才可以大幅度的縮短整個生產線的產出時間,提高整個生產線的總體效率。比如說:通過技術改造,把生產線上不同的流程連接在一起,實現(xiàn)單件流的流水線生產,同時把生產的批量減少到原來的20%,那么,整個生產線的產出時間立即就減少到只有2天左右,想比原來的10天,改善了80%。 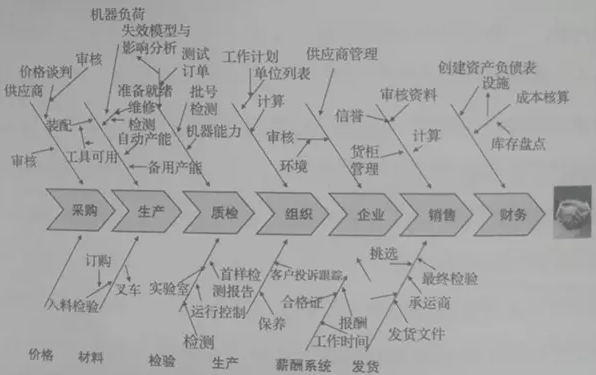
圖3 各種流程的干擾 生產線上的浪費可以通過價值流程圖分析非常直觀的看出來,但是如果站到整個工廠管理運營的角度去看,生產又只不過是整個工廠管理運營中的一個環(huán)節(jié),把價值流程圖分析抽象放大來分析整個工廠的運營管理,我們可以得到一個如圖3所示的鏈狀的管理運營流程圖。從這個圖中可以看出,大量的無法準確計算時間的管理活動充斥其中,各種影響因素是數(shù)不勝數(shù),生產這個唯一真正增值的環(huán)節(jié)顯得毫不起眼,大量間接管理流程活動產生的數(shù)據(jù)的汪洋大海,里面充斥著各種類型的浪費,吞嚙了寶貴的時間,耗用了大量的資源。這個時候就會發(fā)現(xiàn),生產的改善變得如此無足輕重,因為它只是這個鏈條里的一環(huán),而每一個環(huán)節(jié)之間的等待,都可以輕而易舉的把生產改善帶來的效率提高輕松吞嚙。比如說,生產線通過改善,減少了三天的產出時間,但是客戶發(fā)來的訂單由于在各個職能部門間的等待,導致一個星期才能更新一次,所以,對于客戶來說,生產這三天的改善,完全感覺不到。而這些在不同管理流程之間等待的時間,具體的小時數(shù)或者天數(shù),也是數(shù)據(jù),卻也總是被人們所忽視,因為根本就沒有去計算,當然是存在卻看不見,但是基層的員工們卻每天都被這些數(shù)據(jù)包圍著。 這也是可以量化浪費的數(shù)據(jù),同樣是精益數(shù)據(jù)。 工四100術語定義 精益數(shù)據(jù)是一種衡量生產流程的時間數(shù)據(jù),是面向一線操作工人的數(shù)據(jù)觀。與工業(yè)大數(shù)據(jù)相對,它不是從數(shù)據(jù)中去挖掘價值,而是從流程價值來分析一手的數(shù)據(jù)何以產生。它為操作工人而存在,反映了生產中觸手可及的流程接口的價值。 傳統(tǒng)的管理都是以功能為導向的,不僅僅是把生產線上同樣功能得機器擺放在一起進行生產,相應的各個管理部門也是依照職能進行設立以及安排工作,人為的造成了流程與流程之間的隔離及等待。比如說,業(yè)務員把需求報告給業(yè)務經理,業(yè)務經理審核及批準后再回到業(yè)務員手中,然后業(yè)務部門的文員再匯總所有的經過核準的業(yè)務需求傳遞給生產計劃的文員,生產計劃的文員再層層上報下傳的折騰起來,看起來人人都忙碌的不可開交。 其實根本在于功能導向管理的天然的缺點,組織之間的隔閡造成大量等待。 針對這樣的情況,在精益思想里面有一個原則,叫做以流程為導向的布局,不僅僅適用于在生產線上,依照產品生產經過的各個流程的需求進行設備和生產人員的布局,這個思想同樣適用于打通各個職能管理部門之間的組織隔膜,通過以流程為導向的方法所擁有的優(yōu)勢,可以持續(xù)調控各個單獨流程之間的連接。從而消除等待,提高效率。 發(fā)現(xiàn)浪費、消除浪費是精益管理的天職,而這些數(shù)據(jù)都是代表著一個個具體鮮明的浪費的數(shù)據(jù),都是精益需要的數(shù)據(jù),這都是可以量化浪費的精益數(shù)據(jù)。 讓數(shù)據(jù)為一線工人服務 豐田的精益管理帶來的巨大成功告訴我們,企業(yè)的競爭力不僅僅是通過最新的技術來創(chuàng)造的,機械設備已經無法創(chuàng)造額外的價值,而是要通過流程來創(chuàng)造價值。而流程,就像軟件一樣,是可擴展的,即無需付出相應比例的額外成本,就可以發(fā)展,而且產生完全不同的盈利效應,消除掉浪費,就是賺錢。 未來的經濟效益,不僅僅是由機器的能力決定的,也是由流程中機器接口的能力決定的。抹平流程的縫隙,堵住流失的金錢在精益思想的指導之下,通過對工業(yè)管理的數(shù)據(jù)進行分析,進而改善。 然而,流程的可測性,和測量數(shù)據(jù)方面的公開性,這是實際操作中最大的弱點。 如果不去認識它,那就不能發(fā)現(xiàn)它; 如果不能發(fā)現(xiàn)它,那就不會測量它; 如果沒有測量它,那就不能管理它; 如果沒有管理它,那就不能改善它; 如果沒有改善它,流失金錢白花花。 因此,不再用看不見的數(shù)據(jù),如銷售利潤或者成本參數(shù)卻確定一個企業(yè)的價值。而是用看得見可以測量的參數(shù),如運行時間、等待時間、停泊時間等,這些數(shù)據(jù),是每一個企業(yè)員工的責任——這才是真正的數(shù)據(jù),和具有實際的經濟效益。包括登記時間(準備時間,也就是訂單被確定,到相應工具被生產所預定如修理時間、拆卸機器等)、停泊時間(生產時間之間等待的時間)、機器占用時間和整個運行時間。 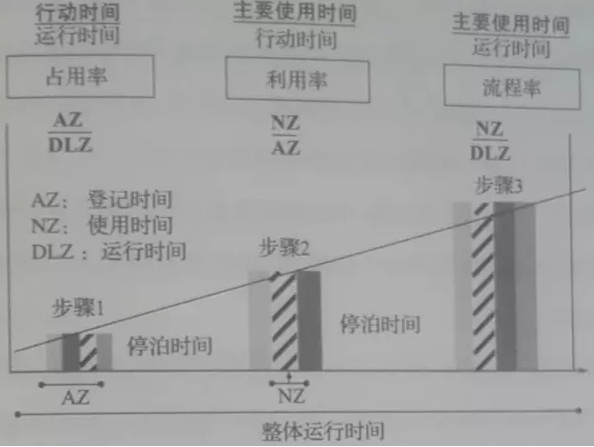
圖4 德國VDMA標準的時間分析 一線員工看的見數(shù)據(jù)和時間,才是精益數(shù)據(jù)觀。這意味著,精益數(shù)據(jù),首先是為一線操作工服務的。 浪費小數(shù)據(jù),吞噬大數(shù)據(jù) 工業(yè)大數(shù)據(jù)在研究數(shù)據(jù)如何產生價值,而精益數(shù)據(jù),則是研究如何產生有用的數(shù)據(jù),它是融入在工業(yè)發(fā)展的每一個階段之中的對數(shù)據(jù)的研究方法,通過精益數(shù)據(jù)的管理思想,可以精準產生有價值的數(shù)據(jù)和準確選擇需要采集的數(shù)據(jù)。 就設備的效率而言,制造需要設備自動化; 就資源的浪費而言,制造需要精益生產觀; 就數(shù)據(jù)的挖掘效率而言,制造需要知識自動化; 就流程的價值浪費而言,制造需要精益數(shù)據(jù)觀。 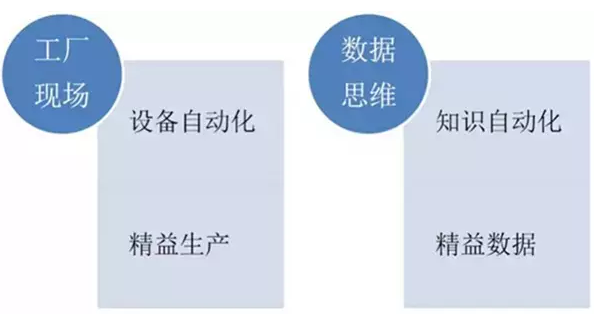
圖5 精益數(shù)據(jù)是一種現(xiàn)場數(shù)據(jù)思維 只有建立價值流程的小數(shù)據(jù)觀,工業(yè)大數(shù)據(jù)的價值才能真正發(fā)揮。否則只是緣木求魚,大數(shù)據(jù)的價值將淹沒在大量無用、無效的數(shù)字海洋中。工業(yè)大數(shù)據(jù)對中國制造而言,還是一件大號尺寸的衣服。面向一線工人的小數(shù)據(jù),才是對中國工業(yè)最為合身的價值點。 作者簡介 王群力,博世中國投資有限公司亞太區(qū)供應商發(fā)展高級經理 林雪萍,北京聯(lián)訊動力咨詢有限公司 精益數(shù)據(jù)-忘掉工業(yè)大數(shù)據(jù)吧 | 責任編輯:蟲子 |